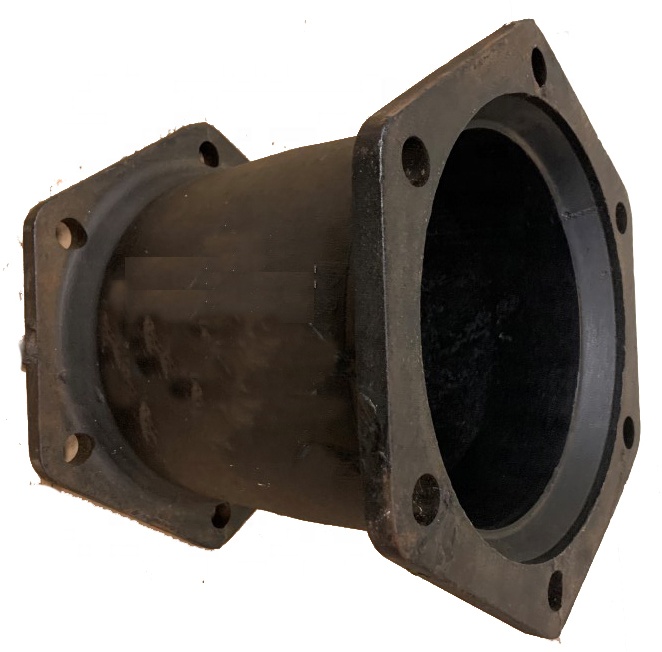
Unveiling the Two Most Common Types of Welds: A Comprehensive Guide
January 22, 2024Welding is a fundamental joining process used in various industries, from construction and manufacturing to automotive and aerospace. Understanding the different types of welds is essential for engineers, fabricators, and welding professionals. In this article, we delve into the two most common types of welds, exploring their characteristics, applications, and advantages.
- Fillet Welds:
Fillet welds are widely recognized as one of the most common types of welds. They are characterized by a triangular cross-section and are commonly used to join two components at right angles or to create lap joints. Fillet welds can be executed on both sides of the joint or on one side only, depending on the design requirements.
Key Features and Applications:
- Fillet welds are versatile and can be applied to various materials, including steel, aluminum, and stainless steel.
- They are commonly used in structural applications, such as bridges, buildings, and machinery.
- Fillet welds provide excellent strength and load-bearing capacity, making them suitable for both static and dynamic loads.
- Their relatively simple execution and cost-effectiveness contribute to their widespread use in various industries.
- Butt Welds:
Butt welds are another prevalent type of weld used to join two components along their edges in a butt joint configuration. This type of weld offers a continuous and smooth joint, resulting in a seamless appearance. Butt welds can be further classified into several subtypes, including groove welds, square-groove welds, V-groove welds, and U-groove welds, depending on the joint design and preparation.
Key Features and Applications:
- Butt welds provide exceptional strength and integrity, making them suitable for critical applications where joint quality is paramount.
- They are commonly used in piping systems, pressure vessels, and structural frameworks.
- Butt welds offer excellent resistance to fatigue, corrosion, and leakage when executed correctly.
- Their versatility allows for the joining of various materials and thicknesses, providing flexibility in design and fabrication.
Conclusion:
Fillet welds and butt welds are the two most common types of welds used in industrial applications. Fillet welds excel in joining components at right angles or creating lap joints, while butt welds offer seamless and robust joints along the edges of components. Understanding the characteristics, applications, and advantages of these weld types is crucial for ensuring structural integrity, performance, and reliability in welding projects.